Racecar Performance Development: The 5 Key Factors (Le Mans Feature)
- Jahee Campbell-Brennan
- Jun 6, 2023
- 10 min read
With the 2023 Le Mans 24h approaching in a few days and the warm up well under way, the 100th edition of this famous race is the first for many of the newly developed brand new LMH and LMDh platforms.
After years of development, it's time for manufacturers to show the world their engineering prowess - an opportunity for the years, months and days of engineering design, development, testing and validation to be displayed to the world. The best teams will emerge victorious.
This makes for a good opportunity to visit the subject of racecar performance development.

These are a total of 7 new chassis’ racing this year, and each has had its own development process, but in that, there are certainly some common engineering approaches and methodologies employed by each manufacturer, so what are they and how are they identified?
In any engineering application, the first task in solving a particular problem is... to understand the problem.
This sounds obvious, and at its core it is.
Motorsport presents a particular engineering problem in which the overarching objective is to achieve the fastest lap time possible within a given set of regulations.
When developing a new or existing vehicle platform, in order to understand where to focus our efforts, we first need to understand where the greatest reward is - what counts in developing lap time gains?
There are countless variables which have input into a vehicle’s dynamics, all with a particular weighting against the overall equation of performance, so a logical start in determining where to focus our efforts is to have a thorough understanding and a method of qualification for all of them.
With this understanding, the strategy of action is an easy output. This is something which applies to any task within any organisation - the crucial activity is in developing a process which enables you to make these decisions with confidence by gathering and quantifying the important things in the environment you are operating in.
Methodologies
In motorsport and other high performance engineering environments, it’s common to develop systems and processes (methodologies) of weighting variables in terms of their salience of influence to the performance objectives. To do this we can classify these variables into the tiers of first-order, second-order and third-order effects to vehicle performance.
Let me not trivialise the difficulty of this activity. In reality, developing a high fidelity understanding of the hundreds of performance parameters of which we have control in our environment is a monumental task. In today’s world, this is rooted heavily in the use of mathematical modelling techniques i.e. simulation.
In top level environments such as F1 and LMH/LMDh development, this is the daily pursuit of dozens of engineers, the cutting edge of simulation & lab testing technology and many cumulative years of experience in the sport.
To give a practical example of this methodology, we can start by looking at the first-order, second-order and third-order classifications of a simple performance attribute - weight/inertial properties.
First-order quantity here would perhaps unsurprisingly be the total mass of the vehicle.
A second-order weight related effect would be the height of the CoM.
Moving down the detail, the moments of inertia in roll, pitch or yaw could be classified as third-order effects.
So, clearly the ‘low hanging fruit’ if we are to be focusing on the vehicle’s inertial properties to find performance would be to spend some time at the top of the hierarchy (first-order) with weight saving measures rather than to spend valuable resource trying to reduce roll inertia (third-order) of the chassis.

I hope this logical approach establishes the premise of these forms of classifications and highlights the importance of establishing robust engineering processes in your pursuits to understand the problem at hand. With a clear and thorough understanding of where to focus energy, we save time, human effort and money.
If we do it better than our competition too, then ultimately we find ourselves further up the grid ;-).
In the following writing, we’ll spend time covering the 5 key factors of performance in race cars and cover some of the theory behind why they hold the importance they do.
Credit Due
Before we start, I’d like to give some acknowledgement to Mike Law, who inspired this article during a conversation we had recording an episode for our recent Vehicle Dynamics Insights Series.
The approach to solving problems in the manner is outlined here is based in a framework Mike has developed which he calls ACE Thinking. Mike has recently written a book of the same title on this.
I personally have found it very useful in developing my approaches to engineering problems in my work and will no doubt find it useful in general life decisions. I would highly recommend it - here is a link.
The Big Five
So, with that said, what are the big 5 parameters we should be watching in terms of vehicle performance development and what are the physical principles behind their importance?
1. Weight / Inertial properties
2. Powertrain
3. The Driver
4. The Tyres
5. Aerodynamics
1. Weight
A large amount of vehicle dynamics is based on Classical Mechanics and the manipulation of forces and moments around a vehicle, so this automatically puts the spotlight on Newtons 2nd Law (Force = mass * acceleration) as a relationship to pay close attention to.

Acceleration is maximised when Mass is minimised, so whether we’re pulling lateral acceleration during a corner, accelerating down a straight or braking into the following corner, a low mass is going to maximise the performance delivered by a given accelerative Force for the entire lap.
This principle is why we always seek to implement light weighting measures to any race car, and is why its unsurprising that regulations have to arrest some of this development. Due to its performance value, manufacturers will happily pour serious money into materials developments which allow grams to be lost. The use, and prohibition of Aluminium-Lithium-Beryllium alloy brake callipers is a nice example of this, very light and very stiff to save grams of weight, but very very expensive.
Moving down the hierarchy, a second-order contributor to performance is the location at which the vehicle’s mass can be assumed to be concentrated i.e. the CoM.
The CoM (Centre of Mass) height from the ground plane dictates the level of weight transfer experienced during lateral and longitudinal accelerations. A higher CoM means more weight transfer.
Weight transfer is an important factor to grasp when we consider the physical properties of the tyre and the influence of a factor known as load sensitivity, which demonstrates that the grip lost on the less heavily loaded inside wheels during weight transfer is not recovered on the more heavily loaded outside wheels and a net reduction in lateral force is seen.
Weight transfer is minimised by keeping the centre of mass as low as possible. This means placing heavy components low down in the vehicle - The majority of the contribution to its positioning is from heavy & bulky powertrain components, but the driver’s seating position is also not negligible.
Moving further down the list of priorities into what could be considered third-order, we look at moments of inertia in the context of the car’s response to accelerations driving roll, pitch and yaw.
All other things being equal, lower inertias mean the sprung mass has less energy for spring and dampers to control during dynamic movements, leading to more favourable weight transfer characteristics and ‘sharper’ direction changes.
As with CoM positioning, powertrain layout defines the major contribution to the inertias. With intelligent efforts in the pursuit of overall vehicle architecture and weight saving, the inertias are minimised by default.
By the time we get trackside, ballast allows some manipulation of the CoM positioning and inertias, but adding more total weight (a first order effect) is always going to have the net result of slowing us down.
2. Powertrain
Traditionally, the powertrain can be thought of as a system whose sole purpose is to generate positive longitudinal acceleration.
In situations where we are not grip-limited, which is most of a lap, the powertrain is the limiting factor of acceleration, so as first-order parameters, it pays (in lap time) to ensure that we’re:
Maximising the power generated at the flywheel for a given quantity of fuel (thermal efficiency),
Ensuring that this power is delivered for as much of the rev range as possible.
Optimising the wheel torque generated by this power through accurately defining the gearing and differentials.
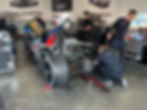
Adequately defining the cooling system such that charge air densities are controlled is a first-order parameter, even more so with batteries and other power electronics in electric and hybrid powertrains.
If the battery system becomes overheated, the powertrain will have reduced capacity to regenerate and deploy electrical power, which certainly carries a huge penalty to performance.
In the days of LMP1 when hybrid power was first introduced, lap time in the order of seconds per lap was being found purely through the development of deployment and regeneration software strategies, so optimising controls and engine maps is certainly a first-order priority.
Second order powertrain parameters would include elements such as the limited slip differential’s operation, traction control, hybrid power deployment and regeneration efficiencies.
Less salient third-order powertrain influences are properties such as shift times and engine service life.
3. Driver
As the commander of the vehicle, the driver has perhaps one of the biggest inputs into performance. An engineering team can prepare the finest vehicle using the latest of understandings in motorsport engineering, only to place dead last or worse yet DNF with a bad driver.
If we assume amongst professional drivers that ability is more or less at the same level, the focus can be directed at the driver’s interactions with the car and the confidence it does or doesn’t give them to extract its maximum performance. This is a substantial part of a development team’s work, both at the trackside and in the office.
At the track, the focus on providing the driver with a car that they are confident with largely means the stability and balance of the chassis must be within comfortable ranges. This is a first-order priority.
The beauty of this is that these are subjective qualities which are experienced differently from driver to driver. The race engineer must always work with the driver to deliver what they want. In Endurance racing where the car must be driven comfortably by up to 4 drivers, this is a challenge.
The driver’s technical understanding is a factor which manifests strongly in tyre management skill. There are driving styles which are great for tyre life and there are driving styles which are not great. Adding further complexity, qualifying efforts require the driver to heat the tyres up quickly for flying laps, while the race requires a more delicate approach to maintain a competitive edge. These could be considered second-order at the professional level.
The driver is a valuable stream of data in the decision making process for the engineer, so It’s beneficial for the driver to have some level of technical understanding in order to comprehend and communicate what they are experiencing from the car and communicate it. This second-order effect can also flow the other way as the engineer advises the driver.
Not neglecting the driver’s comfort, cabin temperatures and seat fit can actually have a big impact into their performance over longer races. Second or third-order, you decide!
4. Tyres
To state the obvious, the tyres are the only point of contact between the car and the track surface, so it pays very handsomely to create an environment in which the tyres are able to perform as strongly as they are capable.
As vehicle dynamists and trackside engineers, all our efforts in performance development can be encompassed in the pursuit of maximising the ability of our contact patches to adhere to the road surface.
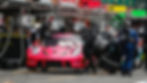
The tyre is a very complex and non-linear component. As a visco-elastic material its behaviour is very strongly linked to both its temperature and its state of degradation (both mechanical and chemical). As engineers, characterising and predicting their performance at any given time is a very difficult pursuit, but one of much reward.
First and foremost, as a first-order consideration with tyres, we must choose a compound which is suitable for the track temperature it will be running on. Getting this wrong will immediately lose seconds of pace, although in modern championships this is dictated indirectly or directly by the regulations.
Tuning of chassis roll stiffness distribution has a first-order influence into the tyre’s environment at each axle. The car is only as quick as the grip limited axle, which makes managing the chassis balance through roll stiffness another crucial setup tool for a trackside engineer to maximise performance, drivability and tyre wear.
The presentation of the contact patch to the track surface in terms of contact area is also of high, but perhaps second-order importance. The kinematics of the suspension and inflation pressures need to be developed to maximise peak performance and overall life of the tyres.
Further second-order effects here include the ability of springs and dampers in managing the energy of the unsprung mass to manage ride performance. Bumps and other perturbances such as curbs will disrupt the vertical load at the contact patch and road surface, which reduces the level of grip the driver can find. Getting the ride setup into the sweet spot is a priority over the weekend.
5. Aerodynamics
Aerodynamics is a major one in a lot of racing series. Higher vertical load on the tyres automatically means more adhesion to the track surface, so it’s a factor which we always want to maximise.
The absolute downforce level and the efficiency (-L/D) of the aerodynamic load is most certainly a first order parameter in performance. In high aero series such as F1, IndyCar and LMH/LMDh, it’s THE first order parameter.
Provided the aerodynamic design is sound, something I’d consider second-order is the distribution of aerodynamic load between each axle, the CoP (Centre of Pressure) location. Being a parallel to chassis balance for its effect on handling, a property we call aero balance is defined by this parameter
Similarly to chassis balance, an incorrect aero balance will produce a car which demonstrates too much overersteer or understeer. Again, a racecar is only as fast as the grip-limited axle.
Not only this, as aerodynamics are speed dependent, this also creates a balance which changes with speed. It’s very important to get this parameter right.
The quality of the vehicle’s aeromap is also of particular importance. This is a measure of the vehicle’s aerodynamic performance as a function of ride height. It’s necessary to adequately control the chassis displacement modes of roll, pitch and heave such that the car is always in a favourable position of the aeromap.
Heave stiffness, roll stiffness and kinematic properties such as roll centre location and anti-pitch geometries are crucial factors in managing the aeromap, but these are less crucial than designing the aerodynamic platform with minimal sensitivity and a wide window in which high downforce is generated.
To give an anecdote on this, in the late LMP1 days, ride height variations of 0.5mm could both be measured in the data and felt by the driver.
Concluding
These 5 categories of performance have been identified through years of experimentation and learning by engineers before me, but that learning doesn’t make the job of performance development simple as it may seem.
Within each of those 5 factors are a huge number of parameters and variables, all taking different
importance in different styles and forms of racing.

With this article I hope I have conveyed that organising these parameters into a hierarchy of performance is a very useful pursuit in race car performance and the objective of focusing resources appropriately, with adequate methodologies.
The aim is to get as far up the grid in the shortest time and the lowest cost!
Also important to appreciate is that a holistic approach is required. A racecar is a complex mechanism of interactions between different sub-systems which all need to be harmonised in order to extract maximum performance.
Engineering is a creative pursuit, and while the science is inescapable, it takes an experienced, mature and agile mindset to win races.
---
You can watch a video of Our director, Jahee and Mike Law talking about the 5 key factors here:
---
If you're engaged in design development or trackside operations, Reach out to explore how we can help.